The new welding procedure test standard, EN-ISO 15614-1:2017, provides recommendations for the measurement and calculation of heat input. In concrete terms, what does this mean for MIG/MAG welding? And how can workshops carry out these calculations in practice?
The requirements set by the standards
Section 8.4.7 of the EN-ISO 15614-1:2017 standard, titled “Heat input (arc energy)”, states the following for the new welding test procedure:
“Users can use either heat input or arc energy (J/mm). Arc energy must be calculated in accordance with ISO/TR 18491. The k factor pursuant to ISO/TR 17671‑1 must be taken into account in the calculation of heat input. The calculation (of either heat input or arc energy) must be documented.”
“Arc energy and heat input both indicate the heat that arises as a result of the welding arc. In the past, these were regarded as alternative terms for the same quantity, but they are now calculated via different formulae. Users can use heat input or arc energy in the monitoring of welds, to be calculated in accordance with ISO/TR 18491.”
The new welding procedure test standard refers to the technical reports for ISO/TR 18491 and 17671-1, which state that arc voltage must be measured as close to the arc as possible. This way, voltage losses caused by welding cables can be eliminated. Table 1 presents the recommended measurement points for various welding processes.
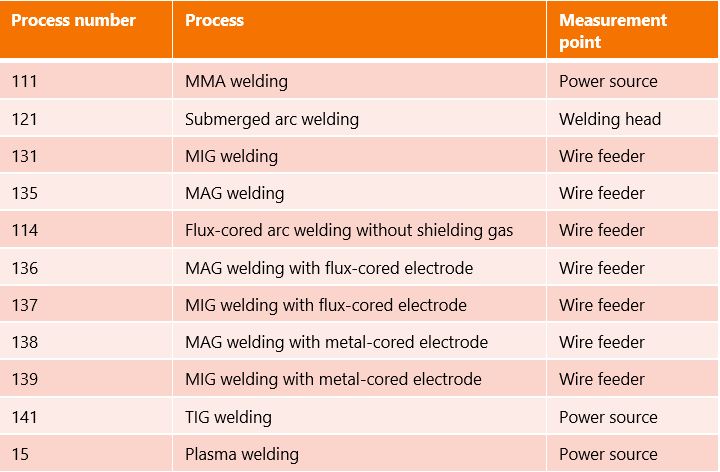
Formulae for calculating arc energy
Pursuant to the ISO/TR 18491 report, formulae A, B, and C are used to calculate arc energy. The terms applied are presented in Table 2.
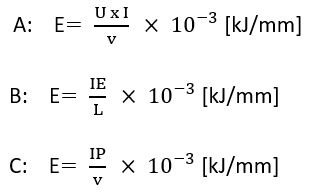
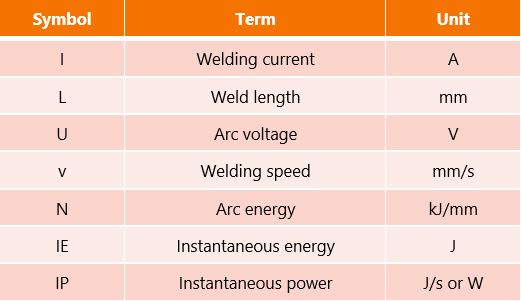
How are the formulae applied?
Formulae A, B, and C are suitable for non-waveform-controlled welding methods. Only formulae B and C may be used for calculations related to waveform-controlled welding methods. Instantaneous energy or power must be measured with an external meter if the welding machine does not display it. In both cases, the sampling frequency must be no less than 10 times the waveform frequency.
ISO/TR 18491 defines waveform-controlled welding thus:
“Welding process modification of the voltage and/or current wave shape to control characteristics such as droplet shape, penetration, wetting, bead shape, or transfer mode(s).”